LUBESAFE COLD CORROSION MONITORING CYLINDER SCRAPE DOWN OIL TEST
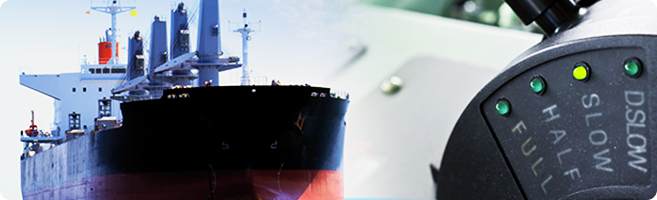
COLD CORROSION SOLUTION for MARINE MAIN ENGINE
Nowadays slow steaming is a hot topic in global shipping industry. A synonym of the slow steaming is reduction in vessel speed. There are difference modes of slow steaming operations: reduced speed, moderate slow steaming, deep slow steaming and ultra-slow steaming. As proven benefits including higher fuel savings, reduction in carbon emissions (CO2, NOx and SOx), improved reliability, and increased efficiency, have been distributed among shipping industry, marine main engine manufacturers approve and endorse ship operators running their fleet under slow steaming modes.
However, one of the major inevitable disadvantages of the slow steaming is the appearance of “cold corrosion” on the cylinder liners, which actually is a sort of corrosive wear causes by acid condensation resulting from a drop in engine operation temperature during the slow steaming mode.
UniMarine provides unique piston underside oil analysis program, Cylinder Scrape-Down Oil Analysis (CSDOA), to shipping industry for dealing with “cold corrosion”. By monitoring parameters of piston underside oil, the CSDOA not only is able to identify cold corrosion of cylinder walls and provides early warning the engineer to be on the alert for “cold corrosion”, but also benefits to other main engine related area such as optimization of cylinder oil feed rate.
Cylinder Scrape-Down Oil Analysis (CSDOA)
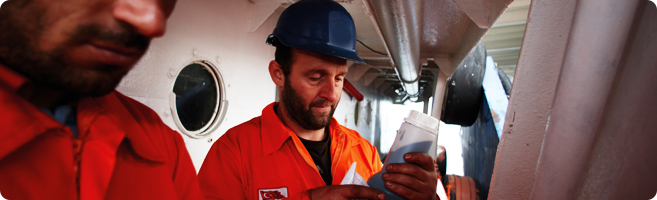
CSDOA monitors following oil parameters:
- Metal Content
- PQ Index
- Element Content
- BN Value
- Additive Level
- Viscosity
- Viscosity Index
- Flashpoint
- Water Content
Features:
- Identifies cold corrosion of cylinder wall.
- Provides early warning to the engineer to be on the alert for cold corrosion.
- Provides comprehensive data on cylinder and rings operation.
- Monitors wear condition of cylinder and rings.
- Figures out optimization of cylinder oil feed rate.
- Monitors condition of stuffing box.
- Identifies contaminants (e.g. water and system oil).
- Avoids over-lubricate main engine.
- Monitor operating condition of cylinder oil lubricator.
Benefits:
- Provides considerable saving.
- Minimises unscheduled down time of main engine.
- Provides preventive measure before
scheduled maintenance of main engine.
- Optimizes operating condition of main engine to meet
load and speed requirement of modern shipping industry.
- Minimises number of renewal of engine components
(e.g. cylinder, rings, and bearings).
- Increases liner renewal interval.
- Extend components life.
- Reduces cost of cylinder oil.
- Minimises contamination of system oil of main engine.
- Reduces potential renewal of system oil.
- Minimises wear of cylinder and rings so as to helps
to ensure proper heat transfer process between the piston
and cylinder wall.
- Reduces operational costs.